For manufacturing organizations, supporting all processes and controlling every stage of development is necessary. It’s not enough to simply create a product; it’s very important to be able to process and analyze all the information to guide the creation of the requested product. PLM systems can help manage all these aspects. They’re widely used in manufacturing, helping manufacturers take a product from development to its entry into the market.
Read our short guide to learn about the importance of PLM, go through the 5 stages of product development, and discover all PLM software benefits for business managers. If you still have questions on how to create a high-quality PLM software solution or integrate the existing software into your business processes, Keenethics is a web company that can help.
The Concept of PLM Software
Product Lifecycle Management (PLM) software digitizes and optimizes all needed information and processes so that every phase of a product has the right objective and outcome. Specialists can contribute their insight, create product tasks, and modify the product to move it to the touchpoint.
The main objective of a PLM platform is to facilitate control over internal manufacturing processes, from design to withdrawal. The PLM software centralizes and documents all product-related data in a cloud-based virtual vault to get all stakeholders access to the single platform and manage the product life cycle. Every department, including cross-functional teams from developers and marketers to salespeople, can plan and execute all aspects of the product life cycle through software through collaboration and iterations. PLM simplifies their collaboration and allows everyone to contribute effectively to problem-solving using product lifecycle management.
PLM software offers a comprehensive view of the product’s lifecycle from multiple angles, allowing in-depth data analysis through a user-friendly dashboard. The software’s centralized data storage ensures everyone benefits from automated processes, secure information, and unified development methods, enhancing engineering efficiency and data security.
The Role of PLM in Manufacturing Business
Since marketing dynamics always evolve, more businesses recognize the need for manufacturing software development, and PLM is one solution that helps companies in several ways. What can PLM do in business? To understand the role of PLM in business, it’s worth assessing its use cases.
I Customer needs
Access to a single data source of truth simplifies many processes. One such way is to provide quality service and maintain reliable customer communication. Access to real-time data makes it far easier for managers to control all processes. If any issue arises, they can easily solve it through qualified collaboration between different departments.
II Time estimation
The platform provides the specialists with alerts, helping them not to overlook important tasks. So, security updates or planned equipment maintenance are done on time through collaborative input through the platform.
III Change management
Any changes are documented in the system. If the specialists find product issues in supply chain management, they can easily specify which factors or changes impact the end work. PLM reduces extra effort and time for employees, allowing them to respond efficiently to supply chain disruptions.
IV Quality
Through systematic tracking and product data management, PLM provides information on quality issues fast. This leads to customer satisfaction, better quality standards, and more reliable products that deliver great business benefits.
V Transparent visibility of performance
PLM is a management tool that collects all critical data on the chain orders and allows managers to control the product performance and how the customer expectations are met. This offers the specialists more insights into improving customer product delivery and using resources and raw materials more efficiently.
The Five Stages of Product Development
Remember, depending on the customer requirements and project vision, each stage can have its path and timeline. Even though product lifecycle project management can’t always be linear, there is a standard lifecycle in development. The stages below show a generic and typical picture of the different stages of the lifecycle.
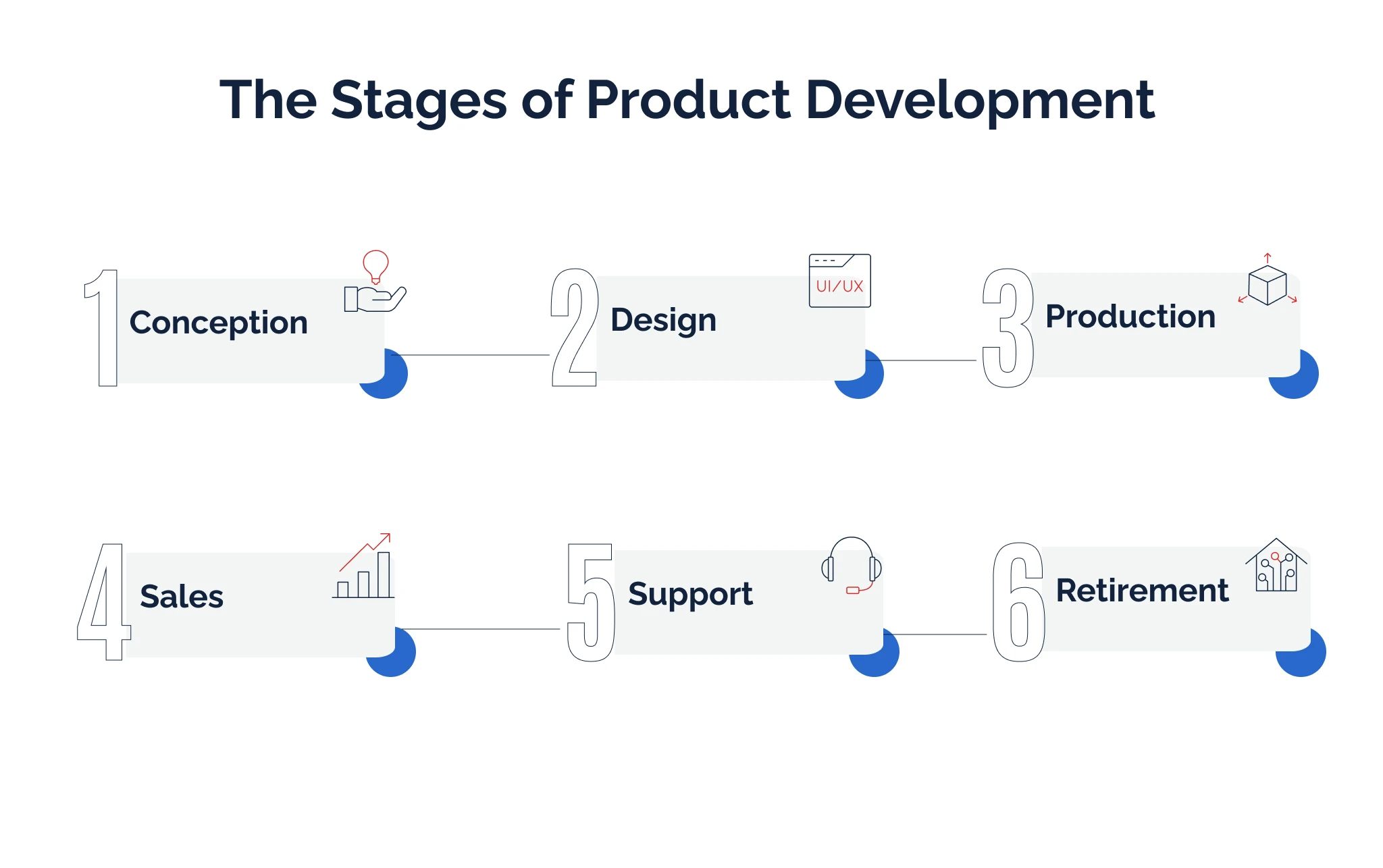
Conception
Forming initial product ideas, defining requirements, and setting specific plans for a new product is always challenging. It requires much work from the client and the development team. At the conception stage, the team conducts market research, analyzes the client’s needs, and determines the project’s complexity. This is the stage where everyone generates and brainstorms ideas for shaping the proper direction of the project.
Design
The design stage involves product planning, prototyping, development, and testing to meet all regulatory and safety requirements. Designing a product that has never been created and tested requires well-established research and development. This phase is important for setting the path for your project by confirming the needed sizing, tech stack, and programming elements, analyzing required systems, and estimating costs for the development. Prototyping helps come to an agreed vision of all stakeholders and a single viewpoint through understanding the project plan template with a timeline and roadmap. With pilot testing, the development team can gather user feedback and integrate proper modifications to improve product demand and usability.
Production
When the company is sure about the product design, it moves to the production stage. The client should consider finding the proper raw materials, assembling components, and testing the final product. Estimating and setting the right design requirements is important at the production stage because doing it at the production stage will lead to project delays, over costs, and frequent refinements.
Sales
When the product development and testing are completed, we can move it to the sales stage. The specialists care about its marketing aspect and distribution to the customers. It must meet all regulations and standards to be ready to set the right pricing models. Usually, the production and sales stages come together since the company should forecast the sales demand for the product to be manufactured. Product launch is not the least critical. It’s the interim where the team coordinates the timing and logistics of the launch, forms a promotional plan, and equips the sales team with the sales tools and tactics to sell the product best.
Support
At this phase, the product is under ongoing support to control and measure the customer experience and collect their feedback. Support helps the company improve gaps and implement more warranties, maintenance, and business strategies to increase customer satisfaction. Tracking product performance is key to getting the expected sales targets. After the sales stage, support is usually an iterative process requiring regular monitoring to adapt the product to market conditions and not only meet the target audience but lead the product to successful, relevant market adoption and sustained revenue.
Retirement
Retirement is the product’s end-of-life phase, which suggests the end of production and support. But it’s not a quick process and a spontaneous decision. The team should first properly evaluate the product’s declining sales, shifts in the market and consumer relevance, profitability, outdated technologies, and functioning. Other reasons include competitive pressure, profitability issues, and regulatory changes.
How do we find out the reason? Specialists from different departments are required to collaborate to conduct a thorough analysis. This happens if the client wants the product to function in the future; based on the report analysis, the team finds areas for improvement and implements needed changes. They can update technologies, interfaces, compatibility, or other aspects to meet customer preferences and adjust the product to maintain its competitiveness, among other alternative solutions.
Benefits of Product Lifecycle Management Software
Maintaining sound product lifecycle management can bring numerous benefits to the company. As we’ve meant earlier, the main condition is extensive collaboration between departments across all product development phases.
PLM helps provide streamlined manufacturing processes, allowing the specialists to better assess product-related flows, procure, plan, and allocate resources, and move the product closer to successful delivery.
Data sharing
The first apparent benefit of PLM is data sharing, which we’ll mention repeatedly. Collaboration between different departments is efficient and streamlined through a single source where the software stores the information. The specialists can effectively analyze the data and consider critical insights they can later use for product improvement.
Better performance
PLM software integrates all aspects of product development processes in a unified system. Employees save time searching for needed data and preventing system inefficiencies. Accordingly, product control is much improved quickly when required information is obtained and the problem is dealt with directly.
Synchronization
The cooperation between engineering, manufacturing, sales, and service is synchronized, allowing all teams to brainstorm and contribute to the project’s success. When there is product compliance, there is little risk. The employees can reduce unforeseen mistakes in any phase through regular monitoring, updates, and quality measures.
Remote 24/7 tracking
Employees can solve any issue at a distance without leaving the location where they are at the current moment. The PLM software stores detailed historical information on changes in product versions related to machinery, customer collaboration, supply, etc. If a high-tech manufacturer finds a problem with the display in a specific machine, they or other specialists can check if, when, and who used the machine for a particular time. It can reduce misunderstandings and help identify the factors leading to tech issues.
Risk compliance management
Requirements and regulations may change while manufacturers may not control or notice. By reviewing documentation and processes in a single platform, manufacturers can efficiently audit what has been achieved and what needs to be done to meet the specific standards and requirements.
Scalability
As the market constantly evolves, any business should be able to adapt to any changes. While there are changes in customer demands and developments in the manufacturing industry, PLM ensures that companies can scale and adjust as required. Manufacturers can develop new parts of the product or improve the existing ones. Add-on modules, customizable workflows, scalable built-in infrastructure, interoperability, and APIs are all aspects that highlight the flexibility of the PLM software. With these features, customers can be sure that their business aligns with needed requirements.
Future of PLM: What Lies Ahead
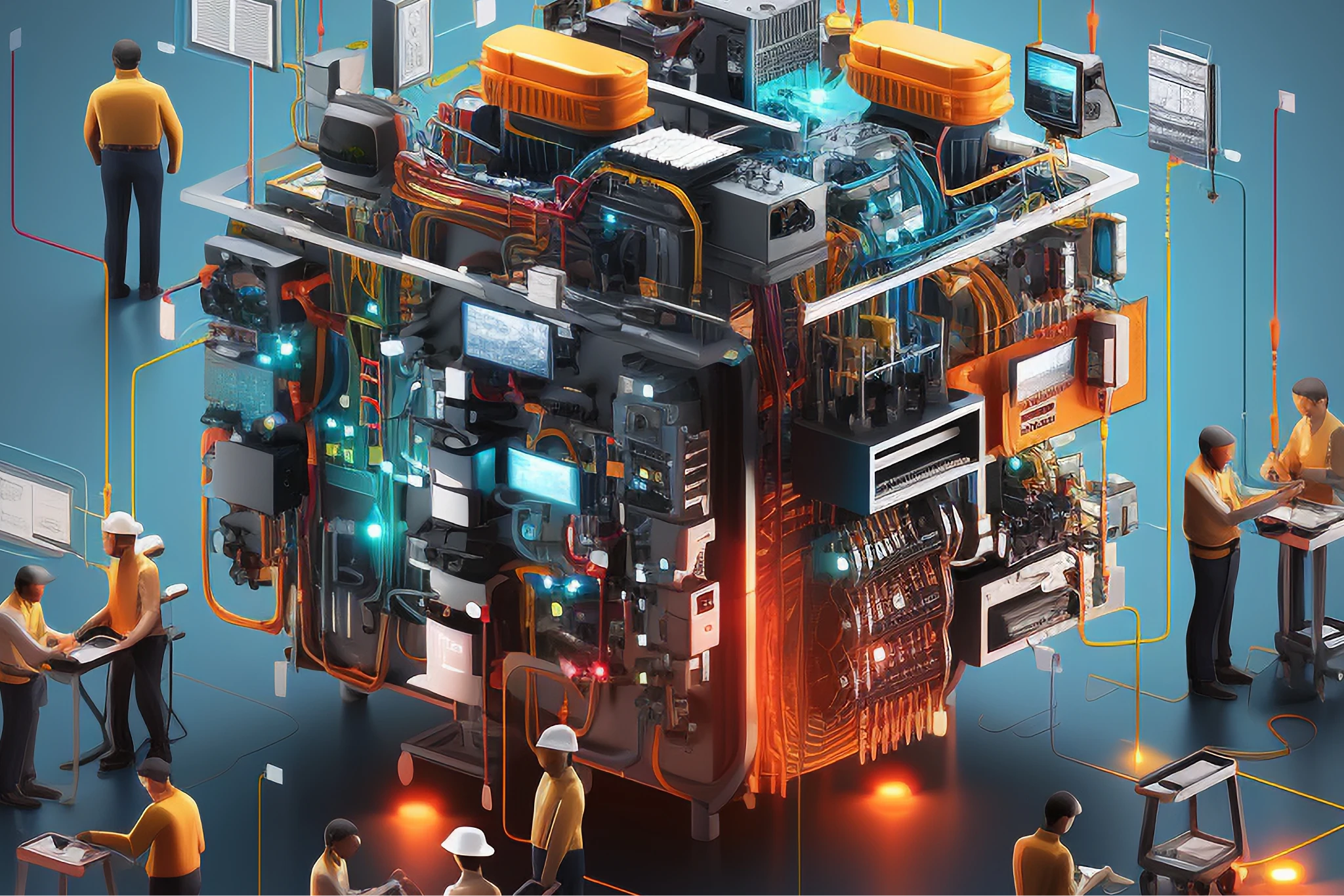
All the trends we present below aren’t new in manufacturing, but they can be more developed soon.
AI
AI continues to analyze a vast set of data and enhance its algorithms. It will revolutionize product lifecycle management by reducing human efforts. By providing manufacturers with analytics, AI will enable the growth of enhanced predictive maintenance and analytics.
Connected devices
Connected devices change how we communicate with products by allowing us to monitor customer interactions and product performance through IoT sensors. Real-time monitoring brings new insights into improving maintenance and operation solutions. Sensors can provide manufacturers with a database for connecting products, maintenance, and requirements management.
Augmented reality integration
When using AR in PLM, developers and designers can visualize and interact with simulations in real-life conditions. AR allows specialists to test new product features, visual design, and convenience and streamline processes like assembly and maintenance. Using AR, manufacturers will have more enhanced visualization through 3D prototyping, saving their time and costs. The single system improves cooperation so everyone can deliver their ideas on immersive presentations in real-time. Also, AR can help train employees through AR training, where the staff should understand some complex processes associated with product development, maintenance, and repair or get some instructional guidance.
Digital twin & thread
By integrating a digital twin, the manufacturers will create a quality virtual replica of the physical product or system to track the performance of the entire product lifecycle. Without losing the quality of the physical product, they can effectively deal with the virtual ones. They can simulate, predict, and optimize product performance under diverse conditions. Just imagine—no more spending costs on physical prototypes. Everything is operated through AR to get more sustained lifecycle management.
SaaS solutions
SaaS solutions have long ago become cost-efficient solutions. Instead of purchasing and installing software on your servers, you can access cloud-based PLM software through a subscription or the Internet. SaaS solutions have the potential to evolve over traditional on-premises solutions. Why? You shouldn’t worry about internal IT costs, like controlling updates, maintenance, and infrastructure. A SaaS provider manages everything without disrupting and preventing manufacturing operations. Saas solutions can scale up or down depending on your needs and demands. And again, global accessibility. What can be better?
Conclusion
Any technology can change the business in a way that will function more technically, effectively, and innovatively. The manufacturers can improve product planning, modeling, and management through the PLM collaborative software, allowing them to unite customers and other stakeholders from all over the globe. All solutions can be proven for their applicability in certain sectors and target audiences. If you’re interested in a PLM solution for your business, we’re ready to provide you with clear use cases for your case. As a strategic process, PLM can improve supply chains and make your business more responsive and adaptable.
FAQ
What is a PLM software system?
PLM software is a system with integrated tools and processes created to help manufacturers manage the entire product lifecycle. Specialists from all departments access data on a single platform and collaborate to enhance product performance and quality and contribute to innovation. PLM software helps companies manage resources, time, and costs relevantly.
What are examples of innovative product lifecycle management?
PLM is used in many industries to improve quality and compliance, reduce time-to-market, and simplify decision-making. It streamlines many complex processes by integrating support into product development’s design, development, manufacturing, support, and sales stages.
- The first example we can consider is the automotive industry. In 1985, the American Motors Corporation used PLM to help engineers design new vehicles. The combination of machine efficiency and human efforts produced the Jeep Cherokee line of cars.
- Boeing integrates data from teams and suppliers through PLM to manage the complex aircraft assembly process in aerospace and defense.
- For R&D management, Pfizer and Johnson & Johnson use PLM to ensure the efficient development of new drugs and therapies.
- Nike and Adidas manage the design phase through PLM tools by integrating feedback from designers, manufacturers, and retailers.
What are some challenges of PLM?
PLM can be difficult for manufacturers to integrate. Considering the vast amount of data, the owners should consult the development team to ease the implementation process with existing enterprise systems, from Enterprise Resource Planning to Customer Relationship Management.
On the one hand, managing data in PLM is easier, but on the other hand, the manufacturers should ensure data accuracy, consistency, and security while accommodating different data formats.
Training employees is also important. While they are accustomed to traditional workflows, employers should provide the needed training to allow them to adopt new processes quickly.
Industry compliance is another challenge requiring accurate documentation, traceability, and regular audits to adhere to industry requirements.
The business owners should be ready to address these and other challenges to get the most benefits of PLM software. Addressing a proven development team can simplify the process of addressing them all. The web development company can help with business analysis, design, testing, and support to allow manufacturers to meet a new competitive edge in the marketplace.
How do you measure the success of PLM efforts?
We can measure the success of PLM software solutions by considering the following points:
- time-to-market from concept to release;
- enhanced performance, which means PLM reduces costs on iterations for many stages, including design, development, and material waste;
- quality improvement, which we get through real-time monitoring of the product quality metrics;
- we get revenue growth and better customer retention rates with the efficiently implemented PLM.
Learn how you can turn your vision into valuable product innovation with Keenethics. Book a free consultation or project estimate.