Do you want to know the core features of inventory management software? This article will explain them!
When creating inventory management software, the relevant decision-makers must clearly outline the core features your inventory management solution should have. Why is this so vital? For custom development, a clear breakdown of features is essential because it allows one to fit the needs of their company during the manufacturing software development. For more general development aimed at the market rather than particular firms, the focus on features is central since it can help cover a larger number of potential customers. Hence, the main goal of the presented article is to help the readers understand what features of inventory management software they need to concentrate on.
What Does Inventory Management Software Stand For?
Before we proceed with the analysis of the features, let’s look at the essence of the presented term. Inventory management software is a set of programs used to manage inventories in various firms. Inventories, in turn, are the collections of assets utilized for the productive activities of a particular business. For example, offices usually focus on assets such as printers and personal computers. At the same time, manufacturing businesses concentrate on machinery and portable tools, which are central to their production process. Inventory management software is important for many reasons.
Firstly, it helps track all the inventory levels of all assets and prevent their losses. When you have multiple tools that require tracking, situations in which they can be lost are common. With inventory management tools, the likelihood of losing some objects in a business becomes exceedingly low. Secondly, inventory management tools are also capable of real-time tracking concerning the status of various machines. For instance, they show their battery levels or problems with certain parts, reporting the information to relevant engineers. This is vital because such an approach allows different firms to minimize the downtime of the involved machines, maximizing their impact on the long-term company profits. Lastly, inventory management tools also help employees navigate item-heavy spaces. One can quickly find the instruments they need with the use of such software. For this reason, the popularity of these tools on the market isn’t surprising.
Key Features Of Inventory Management Software
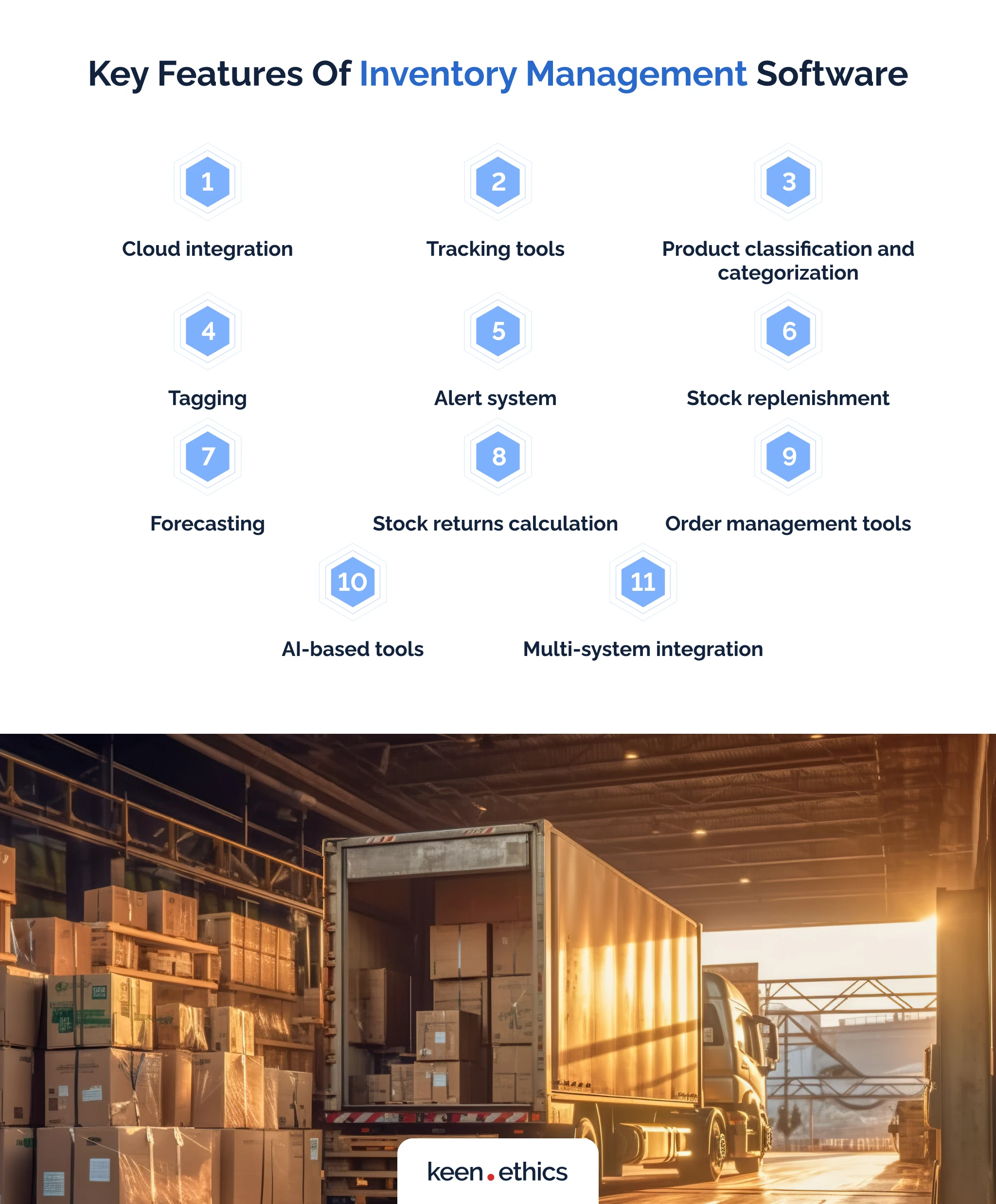
Modern inventory management software features are highly diverse. Here are some core elements to consider in this respect:
1. Cloud integration
The first vital feature of any high-quality advanced inventory management app is cloud integration. Why is this the case? Cloud integration is crucial because it allows one to use a certain app from any location. Many manufacturing companies have to split their activities across several locations, which reduces inventory accuracy. For example, they may have separate warehouses and production facilities. In this light, storing everything in the internal networks is a costly and time-consuming approach. A cloud, however, allows the workers of a certain firm to access the core production data from any location. As a result, inventory management functions become possible across numerous core facilities.
The time-saving and cost-minimizing aspects of inventory management are potent here: with cloud technologies, you can choose locations that are of benefit to you instead of focusing on their ability to connect with other facilities. As long as Internet access is available, cloud technologies enable you to perform the majority of the relevant actions.
2. Tracking tools
The second core feature of a high-quality inventory management app is undoubtedly high-quality tracking. Tracking within inventory management software features can take different forms. Firstly, you can use the worker-oriented report approach. Workers who take a particular tool get an opportunity to report that they’re using it via this system. Secondly, if you’re afraid that the workers may fail to report certain data, there’s also an option of using a combination of hardware and software. In this respect, many firms are offering the integration of the so-called RFID and GPS hardware.
These are trackers that allow one to automatically identify inventory items and, more importantly, track them from any location as long as Internet access is present. With these instruments, the likelihood of losing certain tools becomes genuinely minimal. There’s also one more positive stemming from the presented use of the relevant technology. Tracking tools are notable for their ability to create advanced usage histories for certain objects. With their integration, you can find out how long a particular instrument was used and how it was utilized, benefitting from effective inventory management. In short, an opportunity to use inventory management apps as instruments for creating long-term work history that may be essential in case of disputes or, for instance, major incidents is present.
3. Product classification and categorization
A big problem with traditional inventory systems that focus on pen-and-paper approaches lies in the difficulty of classification for various product types. Many manufacturing firms are producing a tremendous number of wares. For example, they may be producing multiple small parts for different cars. In this light, you risk losing track of certain products: this challenge can easily lead to some long-term losses of revenue.
How can one overcome the presented issue? Electronic inventory management functions are a solution. They enable user-friendly product classification and categorization, making it possible to work with dozens of categories without an overwhelming amount of paperwork. More importantly, their focus on worker-focused tracking (apps like ToolSense offer workers full-scale software for recording the core activities) is also central. It decentralizes the task of tracking and, hence, removes situations in which managers have to deal with multiple types of inventory that they don’t directly oversee in the course of their everyday work.
4. Tagging
Tag systems are a major part of inventory management software features. Why is this the case? Most inventories hold hundreds, if not thousands, of objects. When met with a particular ware, the managers in question may have no idea what they encounter. Tagging and barcoding systems exist to solve the presented problem once and for all. How do they achieve this goal? Primarily by assigning every object in the inventory tracking system a clear number that provides a link to its description.
In pen-and-paper systems, the presented information has to be stored in journals and other types of written records, making the process of finding out information about certain elements difficult. With modern inventory management systems, the situation is highly different. How exactly? Primarily because they store all information in the cloud. Thus, you can scan a barcode and then receive all the core data about a certain tool or product type via an app. This approach greatly speeds up logistics from all standpoints. In instruments like ToolSense, for example, it’s possible to generate QR codes for barcoding and tagging and then quickly scan them to receive all the necessary information on the core objects.
5. Alert system
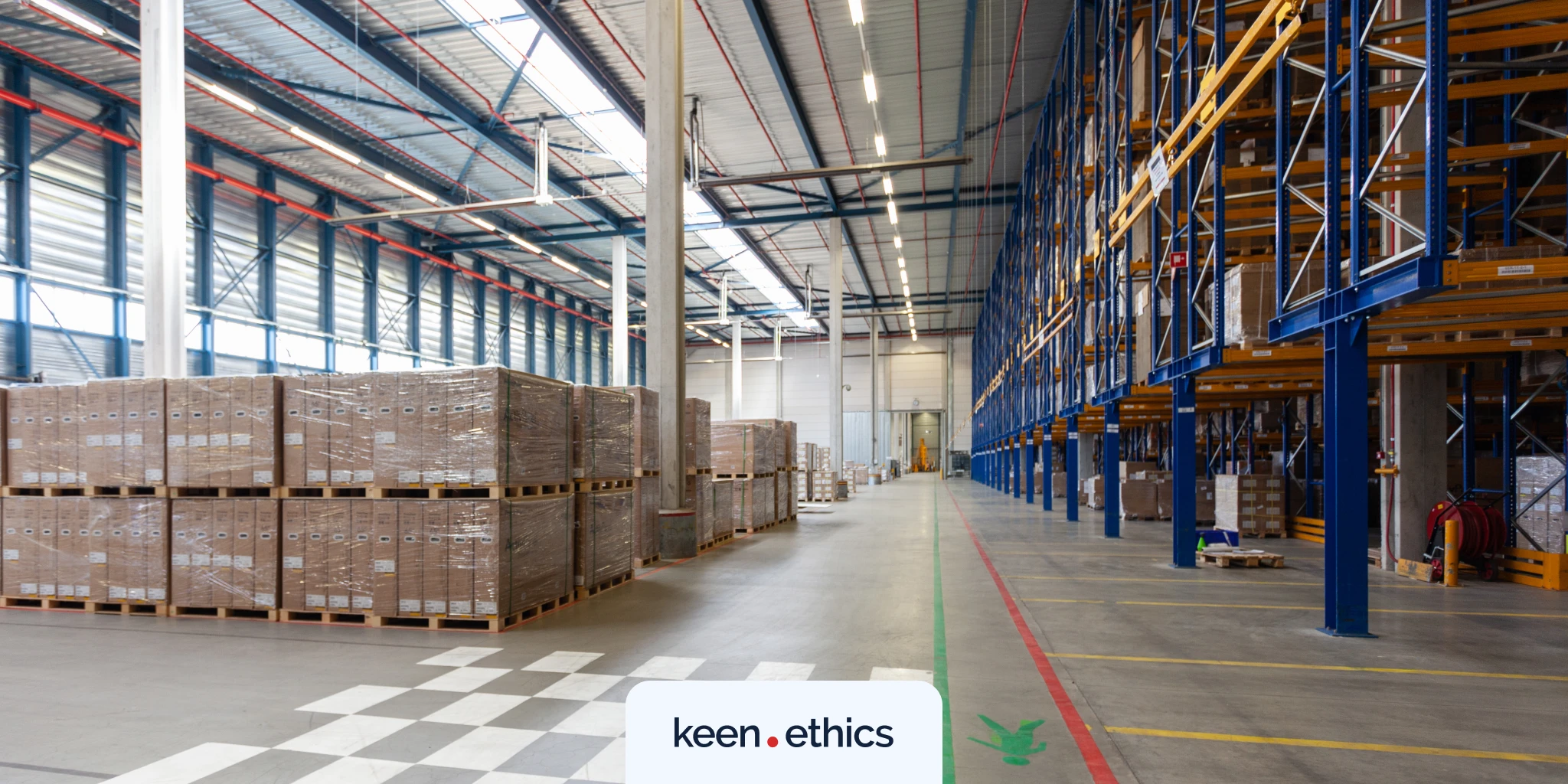
The problem with pen-and-paper frameworks lies in the complexity of tracking all changes in the relevant systems. For instance, let’s imagine you have to track the battery levels of a particular tool. To do this successfully, you have to either ask certain workers to record the data in a journal or do the tests yourself. This seems to be acceptable at first, but major issues arise once these systems start to encompass hundreds of such tools. The maintenance engineers have to constantly check their reports to understand whether one or the other object is failing. In this light, situations in which certain tools don’t work because they don’t get sufficient maintenance are common. A lack of updates or an overwhelming amount of data can lead to situations where maintenance workers will take several days or weeks before they reach a dysfunctional tool.
Alert systems in advanced inventory management software solve this problem once and for all. They immediately inform the maintenance engineers about the most important failures in various production systems. As a result, it’s possible to quickly dispatch help, and relaunch certain machines and tools fast. In this light, automatic maintenance updates are also realistic. For instance, if you know that a certain screwdriver needs to be recharged every two weeks, you can get updates about this action periodically. All in all, such an approach allows one to respond to emergencies with greater performance than in the past.
6. Stock replenishment
Modern manufacturing firms (and even offices, for example) rely on numerous consumables. For instance, a tire production firm may need some materials planning. In turn, an office can require a constant flow of paper and printer ink. We’ve all, regrettably, encountered situations when such consumables run out. This problem easily leads to avoidable time and resource costs. The larger a company is, the higher the likelihood that the relevant resources won’t arrive on time.
Stock replenishment systems in modern inventory management software are a solution to this problem. What exactly do they do? Stock replenishment systems are significant because they can automate the orders for various consumables or, for instance, offer reminders to the inventory managers in an office or a production warehouse. These systems automatically track the number of important objects like ink cartridges through personal reports or even RFID. As a result, you have to spend less time on the analysis of your stocks. Inventory management systems are capable of doing this automatically, reducing the downtime in your business even further than in the past.
7. Forecasting
Our experience shows that all firms have a certain style of doing business. For example, particular companies focus on production during the winter holiday period. This is common for sweet producers or toy sellers. In other cases, businesses may focus on the summer period: this is essential for companies that produce summer/early autumn clothing. More complex situations can involve the fluctuations of customer demand touching upon smaller periods: they may change even every two weeks. Hence, a company that has enough tools for tracking the relevant information can create full-scale predictions about its future sales trends.
Pen and paper systems enable many companies to do exactly that. However, they have major limitations: humans can analyze only a limited amount of information; more importantly, humans are prone to calculation errors in the majority of cases. This data means a computer system can further improve your ability to forecast information and then change supply chain management according to these predictions. Modern AI may even find trends you’re unaware of. Hence, the use of these systems is a perfect way to save resources.
8. Stock returns calculation
Every business needs to know whether this or that element of its stock is profitable for it. Intuitive calculations made from observation or basic calculations are often misleading. They don’t consider many exogenous factors. Consequently, situations in which certain firms use tools that are unprofitable or produce wares that are low-value tend to be common. In the era of pen-and-paper systems, finding those problematic investments was highly difficult. This situation is now changing due to the rise of novel tools. Modern inventory management software features can calculate a tremendous number of factors related to certain products or fixed assets. In this light, you get an opportunity to save a larger number of funds with the use of such tools. AIs, which are becoming increasingly popular today, are noteworthy for finding connections in places where most humans don’t see them.
9. Order management tools
Most manufacturing companies work on an order-based approach. They get a certain contract from another manufacturing firm and then have to concentrate on fulfillment. In the case of oligopoly markets, order management tools don’t need to be complex. One usually works with a few suppliers (in many cases, a singular firm) and has an incentive to deliver them one core ware. This approach enables many businesses to maximize the quality-cost balance for their products. However, not all markets are oligopolies that focus on large wares.
Certain markets promote major diseconomies of scale, where large-scale production only makes things worse. In this light, a manufacturing firm may concentrate on hundreds of small orders, which are typically easy to lose. Order management tools in inventory apps are noteworthy for their ability to track this information. They can be combined with alert systems, for instance, to maximize the long-term performance for all stakeholders.
10. AI-based tools
In our opinion, AI is the tool that will offer a clear delineation between strong and weak inventory control software in the future. Why is this case? As we’ve mentioned before, modern AI can find connections in places where humans don’t see them. This happens for two reasons. On the one hand, AIs are capable of analyzing a much larger amount of information than other systems. On the other hand, AIs are also notable for their ability to create elaborate information networks. Thus, the use of AI is among the best ways to ensure the efficiency of analysis for future inventory management systems. AI-powered frameworks can offer advanced features like predictive analytics, automation, and real-time visibility into supply chain management processes.
In this regard, AI systems can do several things well. Firstly, they may provide great analytical information to the users. Secondly, they can deliver predictive information about certain elements of inventories. Many prediction-oriented systems are focused on the usage of modern artificial intelligence tools. Lastly, AI frameworks using the so-called generative approach may also focus on offering full-scale guides into certain inventories for the users. In this respect, they can act as user information systems. Therefore, we believe that modern AI is among the core tools for promoting an information revolution in the manufacturing sector, enabling better supplier management and optimizing customer service through improved demand forecasting.
11. Multi-system integration
The final feature that all inventory management systems require is the focus on multi-system integration. Various manufacturing firms are using numerous systems for tracking their activities. For example, there may be enterprise resource planning apps within them. Why is integration so important, then? Many of those additional systems have information that can be vital for an inventory management framework. For instance, ERPs often possess a significant amount of data on the demand and supply for various users. This means that you can exchange knowledge between those systems to maximize their value. Consequently, we heavily recommend most firms in the manufacturing sector to actively look for integration capabilities in inventory management systems.
They’re a perfect way to save resources spent on different types of inventory management software and improve overall security and inventory accuracy by consolidating data from multiple sources. Additionally, integrated systems can provide better visibility into various sales channels and help optimize procurement of raw materials based on real-time demand signals, ultimately leading to higher return on investment (ROI) for businesses.
Must-have Quality-of-Life Features for Manufacturing Apps
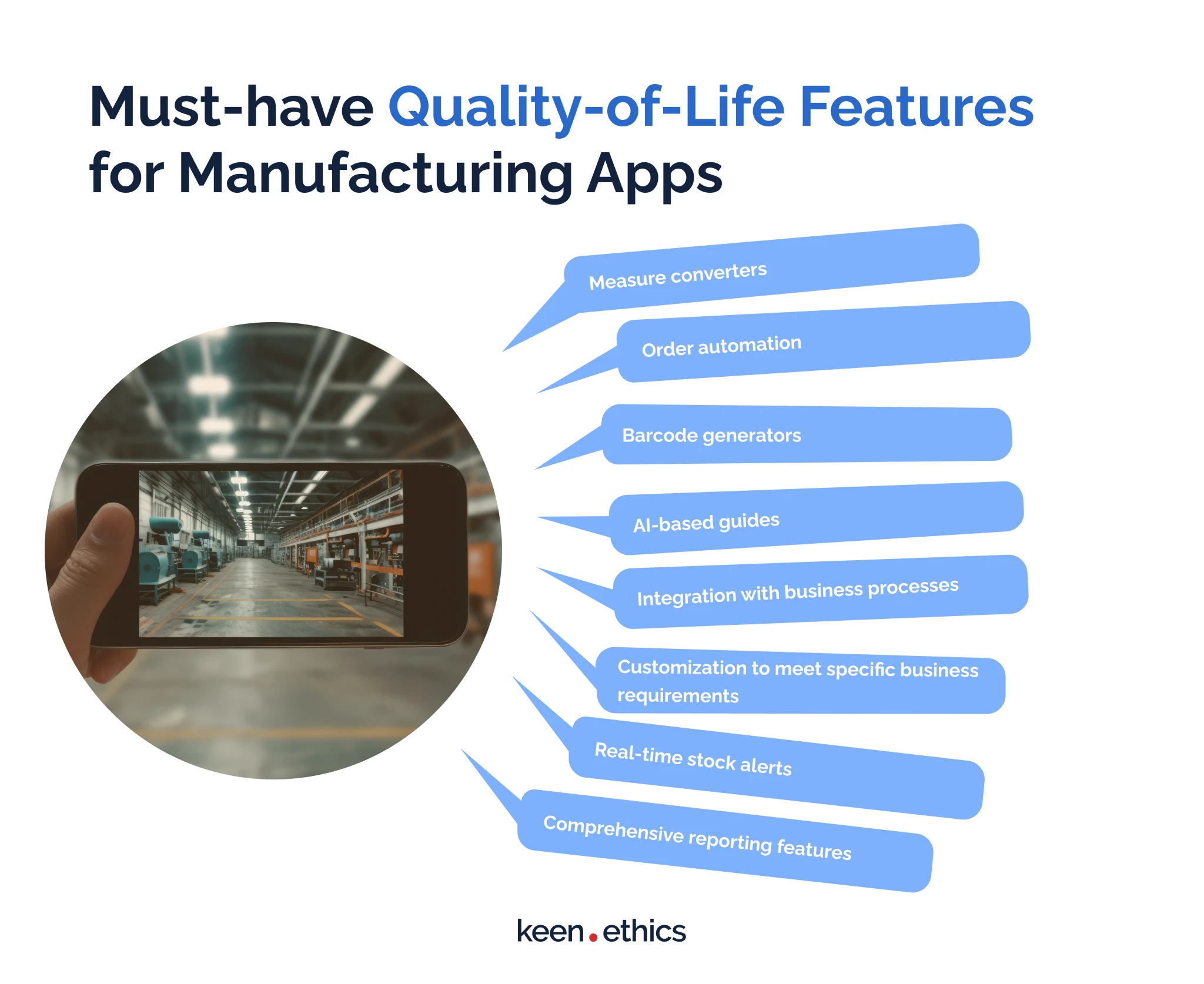
In our opinion, manufacturing apps can benefit from a set of so-called quality-of-life (QOL) features in addition to the core elements outlined above. What are those QOL features? Here they are
- Measure converters: it’s a good idea to have tools that enable you to convert different units of measure. For example, your business partner may be using pounds instead of kilograms. A measure converter within an inventory management app will minimize the pains of working between two systems.
- Order automation: certain objects are used so often and so predictably that you can automate every aspect of their usage.
- Barcode generators: automatic barcode generators can save a lot of time during the stock tracking process.
- AI-based guides: modern AI tools allow one to use them as guides for certain systems. This is exactly what we recommend as a QOL feature.
- Integration with business processes: inventory management software should seamlessly integrate with other critical business processes like accounting, manufacturing, and logistics to ensure end-to-end visibility and control.
- Customization to meet specific business requirements: the software should be flexible enough to accommodate unique business needs and workflows, allowing for customization of features, reports, and user interfaces.
- Real-time stock alerts: receiving timely notifications when stock levels fall below predetermined thresholds can help avoid stockouts and enable proactive replenishment.
- Comprehensive reporting features: detailed reports on current stock levels, stock movements, expiration dates, and other relevant data can provide valuable insights for informed decision-making.
Summary
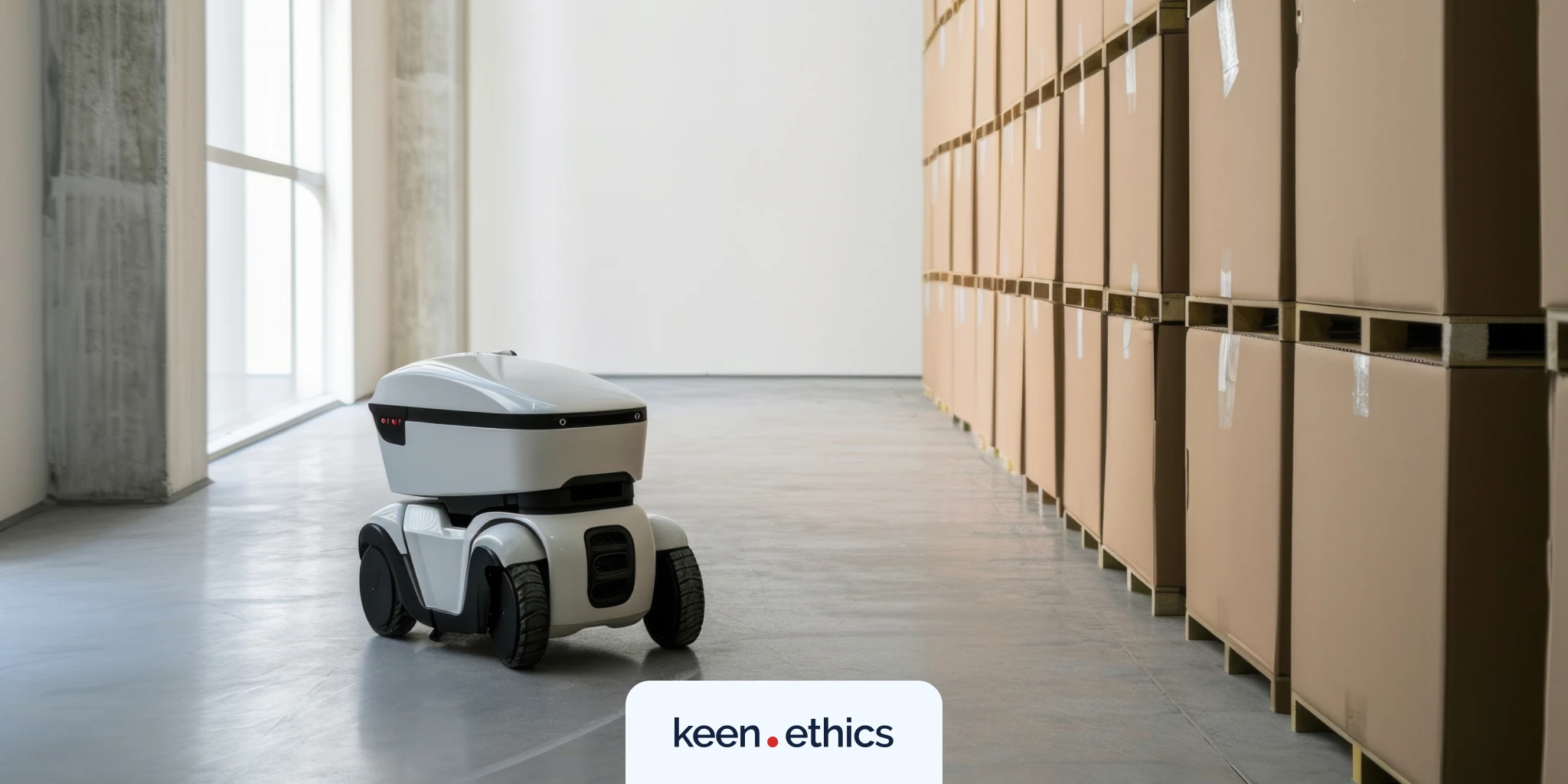
To summarize, modern inventory management tools have a clear set of features that makes them superior to systems based on the usage of pens and paper or, for instance, spreadsheets. Consequently, we highly recommend investments in such systems for the majority of the users in manufacturing spaces. Many office-based environments can also benefit from these systems in case of high inventory loads.
Keenethics is here to help you!