In this article, you’ll learn how to work with ERP manufacturing systems.
Enterprise resource planning is a complex field since the relevant software involves control over entire companies. For this reason, many manufacturing organizations seek to implement this type of software. ERP solutions in manufacturing are notable for giving an overarching view of various companies and the way they function. The main goal of this article is to offer the readers an insight into manufacturing ERP systems. After reading this material, you’ll have a clear understanding of the positive and negative aspects of this technology, as well diverging types of its application in different firms. Spoiler: manufacturing ERP software is a worthwhile investment because it offers an opportunity for an in-depth review of every business process.
What Does ERP Stand For?
The best way to begin a review of ERP for the manufacturing industry is to understand what this technology stands for. A typical ERP is a technology that enables a firm to get complete insights into all its activities. An Enterprise Resource Planning platform uses modules for diverse tasks like inventory management, human resource control, and financial flow operations. In short, the main goal of such software is to give your company full-scale insights into all operations and, more importantly, connect different reports into a singular picture of your firm. By focusing on this information, you can later create elaborate schemas for analyzing customer satisfaction or the need for raw materials. All in all, ERP is a general dashboard that provides a full review of your business operations. The main reason to sign a contract with an ERP provider is the ability to promote best practices in your firm. When you know what happens at every level, it’s much easier to promote reforms.
ERP Systems Benefits in Manufacturing
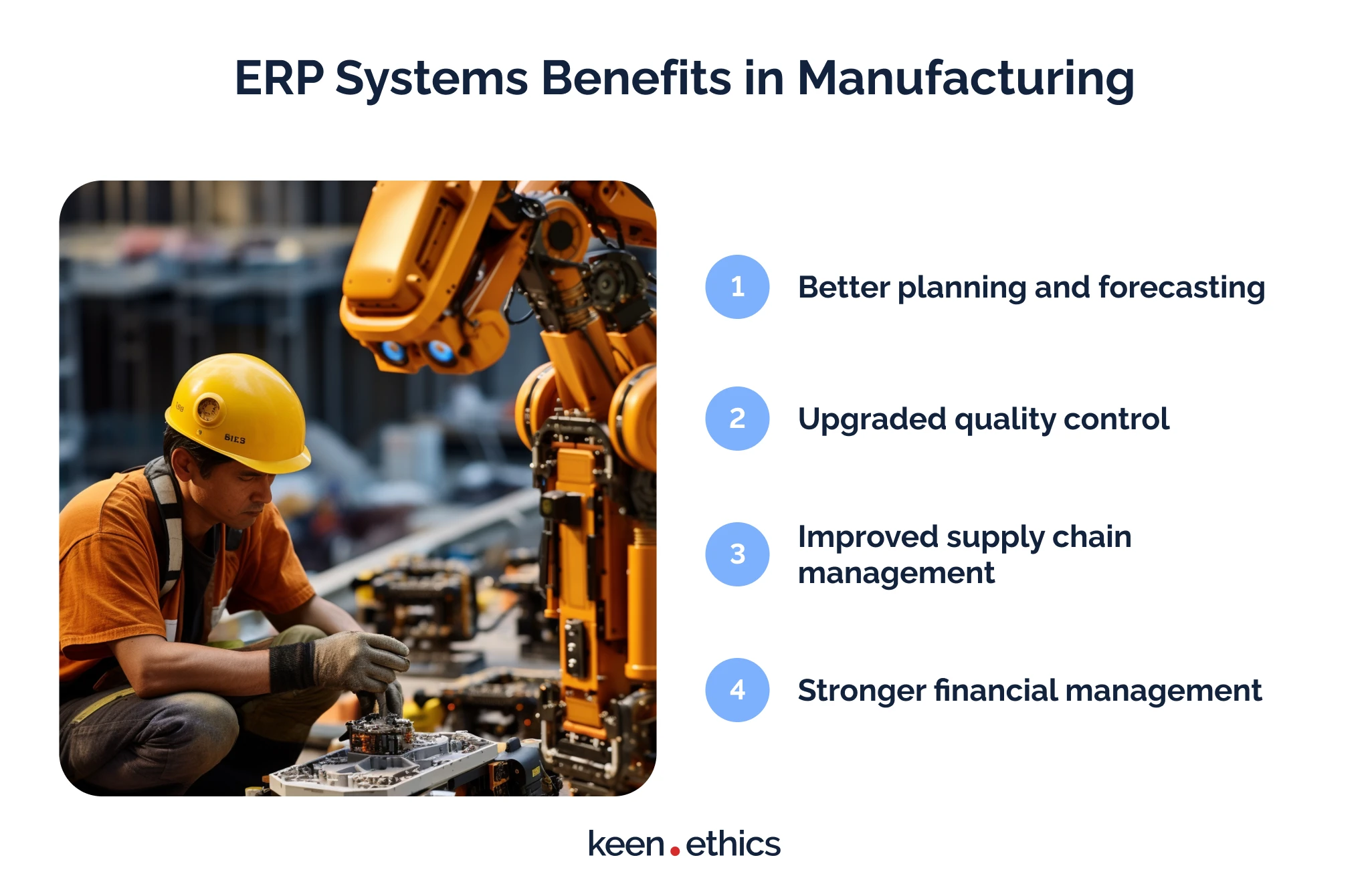
Modern ERP systems have a large set of benefits for the manufacturing field. Let’s look at the core benefits of ERP:
Better planning and forecasting
The best way to improve all types of forecasts is to have a steady supply of information for them. In short, the better information you have, the more accurate various forecasts become. A manufacturing enterprise resource planning (ERP) system is necessary for enabling this effect in the first place. What does it entail? The best manufacturing ERPs offer a general review of your manufacturing processes. Thus, it’s easier to collect information on different activities and turn them into valuable insights capable of transforming the core patterns of behavior in your firm. For instance, you can find out what type of human resources are lacking and then concentrate on closing the respective gap to make your firm more potent. One can predict customer demands based on the preceding periods of production with the help of an ERP platform. All in all, technology is a perfect path for organizing the majority of the manufacturing processes in your business.
Upgraded quality control
ERP for the manufacturing industry is also noteworthy for its ability to enhance quality control for most firms on the market. How does this technology achieve this goal? Above all, through a focus on data collection. ERP allows collecting data about a tremendous number of production workflows. In short, you receive real-time visibility for the majority of the processes through a cloud-based ERP. This approach enables you to upgrade the said processes by remaking production schedules or, for instance, changing supply chain management to include better materials. Moreover, the presented technology has one more positive tendency: you can collect customer reviews and immediately connect them to product profiles to identify problems with them as soon as possible.
Improved supply chain management
ERP for manufacturing industries is also essential for upgrading all types of financial management. How do they achieve this goal? Primarily, ERP can help by giving you a much deeper view of financial flows than other tools. Instead of having insights into the outcomes of financial operations, you can review every element of them in combination. It’s possible to trace the history of all spent dollars and see what Return on Investment these financial operations offer. In our opinion, the core reason to use ERP applications is their ability to provide a single source of information for every worker activity.
Stronger financial management
ERP for manufacturing industries is also essential for upgrading all types of financial management. How do they achieve this goal? Primarily, by giving you a much deeper view of financial flows than other tools. Instead of having insights into the outcomes of financial operations, you can review every element of them in combination. It’s possible to trace the history of all spent dollars and see what Return on Investment these financial operations offer. In our opinion, the core reason to use an ERP is its ability to provide a single source of information for every human activity.
Key ERP Features Aimed at Manufacturing Companies
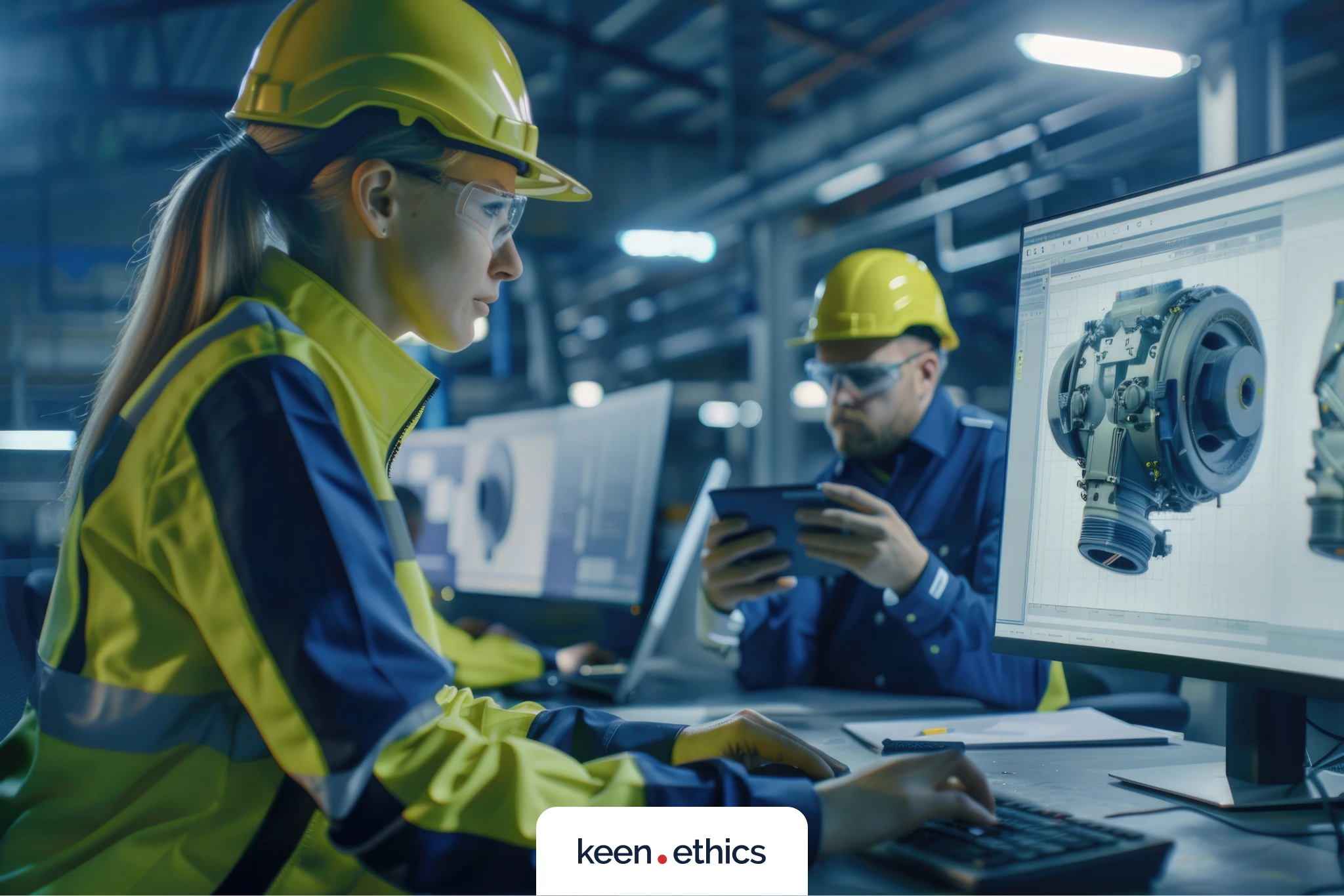
Modern ERP implementations in manufacturing have several features that make them perfect for core business processes in this type of firm:
1. Manufacturing-centric functions
Many ERPs in the production industry offer a wide range of manufacturing features aimed specifically at manufacturing specialists. What are those features? Above all, the integration of various tracking devices. For instance, you can integrate RFID or GIS frameworks to collect as much information about your manufacturing business as possible through enterprise resource planning software. One can also integrate modules for controlling all types of systems via manufacturing ERP features. Therefore, the presented frameworks are strong at upgrading manufacturing operations through a steady flow of information.
2. Planning/scheduling features
Manufacturing relies on a clear set of plans and schedules for efficient business and manufacturing processes. In this respect, modern manufacturing often requires an ability to produce certain wares within deadlines that are minutes — rather than day-long. For instance, car manufacturers often rely on just-in-time production, where parts arrive right when needed to minimize expenditures on warehouses of all types. ERP for manufacturing industries, ultimately, features advanced tools for performing this set of tasks. It has many scheduling frameworks that make it possible for decision-makers to optimize their processes in terms of schedules. You can choose from a wide set of scheduling frameworks, including non-manufacturing approaches such as Agile, which may provide interesting results if tested within the manufacturing field.
3. Inventory management tools
Inventory management tools represent one more aspect of the manufacturing process that is included in modern manufacturing ERP systems. In this regard, you can use ERP tools to manage your inventories. ERP for manufacturing has instruments for a wide range of inventory management tasks. Firstly, it features inventory tracking tools. You can review the levels of certain supplies and make adequate judgments on their completeness. Secondly, manufacturing ERP software integrates various equipment tracking instruments, which allow you to understand if this or that element of an inventory is in a good state. For instance, you can track the downtime of certain devices to ensure that they bring maximal value to your firm. Generally, ERPs are tools that possess all the instruments required for a manufacturing sector. Their goal, in many cases, is to create an all-encompassing framework for controlling a business.
4. QA instruments
Quality control is among the most important elements for any business. The reason for this inference is simple: if your wares are low-quality, there’s a tremendous risk of undermining customer expectations and, as a result, creating a negative image of your product among the clients. A negative image, in turn, can have a long-term damaging influence on your firm, which may eventually lead to its closure. In this respect, ERPs allow tracing every part of the QA process. Firstly, they’re notable for collecting real-time data about various processes. With this information, you can quickly realize the core deficiencies in your production frameworks and the respective manufacturing needs.. Secondly, they can track customer reviews and, more importantly, sales tendencies during the process of implementing an ERP.. In this way, the average ERP user gets an opportunity to clearly understand the causality of certain changes. Hence, ERPs are among the best instruments for enhancing product quality in your firm.
5. Full firm overview
A major issue with traditional pen-and-paper systems is that a lot of information is lost within them. Sometimes, it’s simply impossible to trace where a certain sum of money went and how it was used due to the tremendous number of documents. Modern ERP systems solve this problem once and for all. How exactly? Above all, manufacturing management software does this through a focus on real-time monitoring. With the help of those systems, you can do cost control even for the smallest expenditures. They offer a full firm overview: the managers get to see even the smallest processes happening in their organization. This approach is essential for process optimization. ERP in manufacturing allows you to follow every regulatory requirement set by the government or your investors through constant review of all existing business systems and processes.
6. Integration of production equipment
Modern manufacturing equipment has strong tools for upgrading operational efficiency. These tools are quite diverse these days. What are they? For example, there is computer-controlled equipment. ERP systems offer integration with the most widespread types of smart factories. Thus, you can, for instance, track the status of various machines through the use of such manufacturing equipment with the help of ERP software for manufacturing. In this respect, a manufacturing ERP solution can serve as a perfect framework for reviewing the uptime of certain machines or even their productivity per hour. This approach will allow you to meet the most complex manufacturing business needs.
7. Analytical reporting
Lastly, a major positive feature of ERP systems is the ability to create elaborate reports concerning certain production-related questions. In this regard, the users can generate such reports due to having access to features like real-time inventory tracking that offer a vision of the entire manufacturing process. Combined, all these aspects allow you to have an overarching view of your firm. With the help of ERPs, you get an opportunity to know how every element of your firm functions rather than some singular aspects. In this light, we recommend those systems to every company that needs a real-time update framework for its goals. Observation of operational problems and strengths is among the best ways to improve production efficiency. ERPs enable this type of analysis for all the relevant stakeholders.
What Types of ERP Implementation Exist?
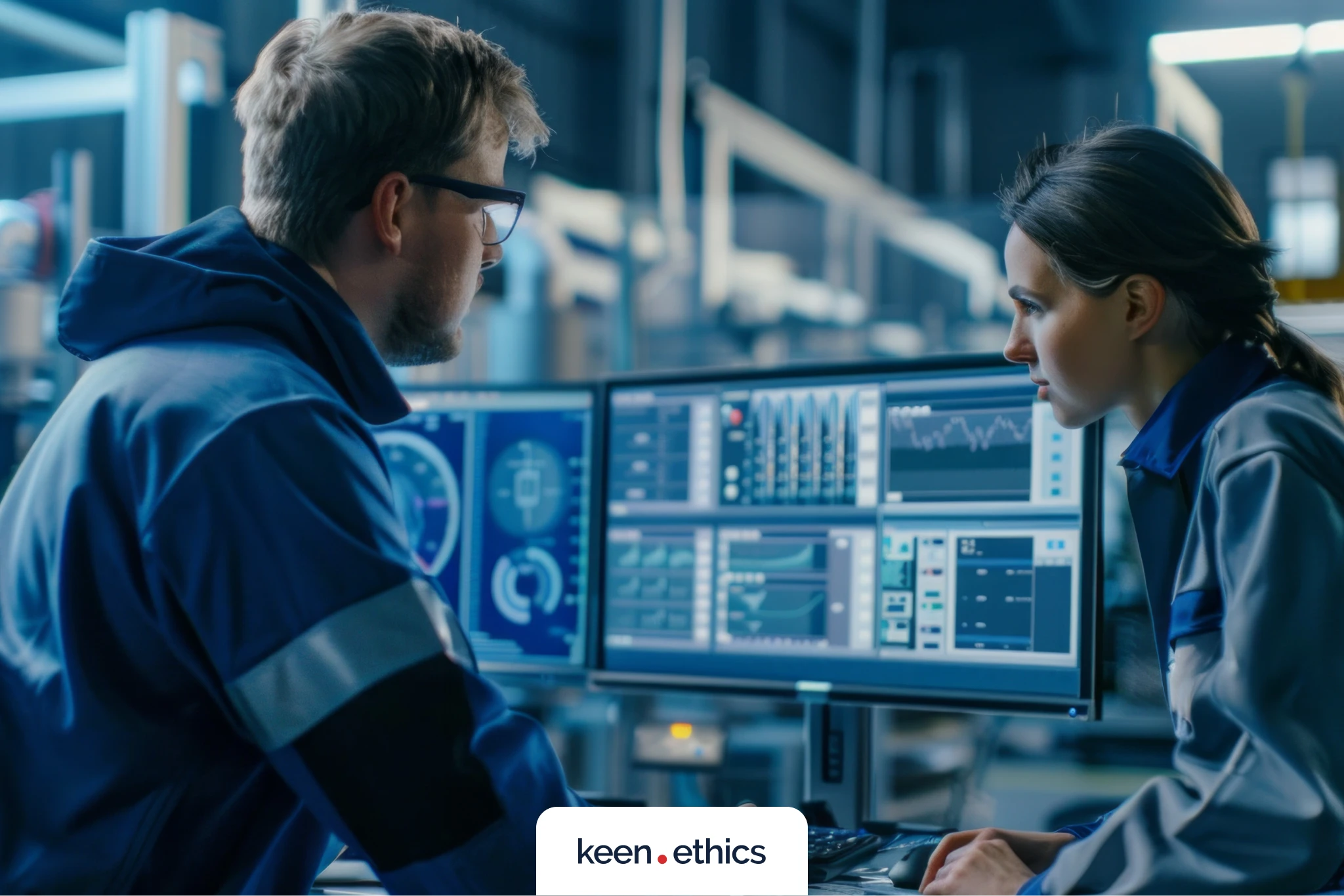
ERP quality standards can be implemented in multiple ways. Here are those ways:
Cloud-based approaches
The most popular type of ERP is cloud-based. In this case, the entire infrastructure of a cloud-based ERP system is situated within a cloud framework, helping minimize operating cost of using a solution. You don’t have to pay for large servers or, for instance, incur the costs of changing various storage devices with cloud-based software. Economies of scale also enable cloud organizations to minimize the costs of electricity and other important resources. Typically, this type of ERP is subscription-based. For instance, Oracle offers its type of ERP to customers through the cloud, asking for a subscription of approximately 600 dollars monthly per worker. The cost of this system is at the higher end as it’s oriented towards large businesses. Nonetheless, there are also smaller systems that also work through a subscription model. In this respect, ERP in manufacturing is noteworthy for a wide range of options that exist on the market.
On-premise approaches
You can also buy ERP systems to then host them on your servers or even develop your solution. In this respect, the benefits of the model primarily have to do with elevated security levels of on-premise ERP systems. For example, a self-hosted system without access to the Internet (only with intranet features) is unlikely to leak data to the competitors about this or that type of a new product. Simultaneously, such systems are much worse at scaling and, in many cases, fail to show the level of performance and feature complexities offered by cloud ERPs. For instance, tracking supply chains with this type of ERP for a manufacturing company is difficult. Detailed insight into outside expenditures may also be impossible in some situations.
Hybrid ERPs
Lastly, there are also hybrid ERP solutions. These are frameworks that involve a combination of cloud and on-premise options. On the one hand, it’s entirely possible to launch these solutions in the cloud, using subscription-oriented platforms. On the other hand, you can buy them to then launch the core features on-premise. Therefore, you get maximal flexibility in such situations. A good example of such a hybrid system is Reflex ERP, which provides both cloud and on-premise tools and platforms for its users. Infor is also among the companies that offer both on-premise and cloud solutions.
Who Needs Manufacturing ERP?
Ultimately, let’s look at the core groups that may need an ERP solution for their business. In our opinion, multiple stakeholders greatly benefit from such solutions these days. In general, they’re advantageous for every part of the market:
Small businesses
Small businesses act in situations where even minor inefficiencies in inventory levels can lead to big problems with their performance. They’re resource-constrained and, hence, require a clear focus on maximal efficiency to survive on the market in the long-term scenarios. In this respect, modern ERP for manufacturing industries is among the solutions that are advanced enough for this goal. They can track resource usage and, ultimately, lead to major improvements in material use efficiency. Small businesses need exactly that to survive on the manufacturing and distribution market.
Mid-market businesses
Mid-market businesses are less resource-constrained and can survive with an inefficiency or two, but often face issues with controlling tasks. For instance, it becomes difficult to review all the activities of the workers in these firms. As a result, there’s a need to focus on solutions that are more flexible when it comes to worker control. ERPs allow for minimizing the reliance on such solutions (for instance, the use of too expansive non-shirking wages, which is advanced by economists) through a focus on a clear control of worker productivity. In this way, it becomes much easier to control a firm and maximize the benefits every worker brings to it in the short- and long-term scenarios.
Large enterprise
Large enterprises face the same problems an average middle-scale business encounters but on an even larger level. Consequently, their core challenge, in many cases, is solved by ERP software used for offering an overarching view of a company. The features that provide Big Data analytics are especially vital. For instance, it’s possible to trace every aspect of customer service and supplier work with the help of these solutions. Thus, ERP software is among the best ways to ensure full control over the manufacturing processes of any business these days.
ERP Implementation Challenges
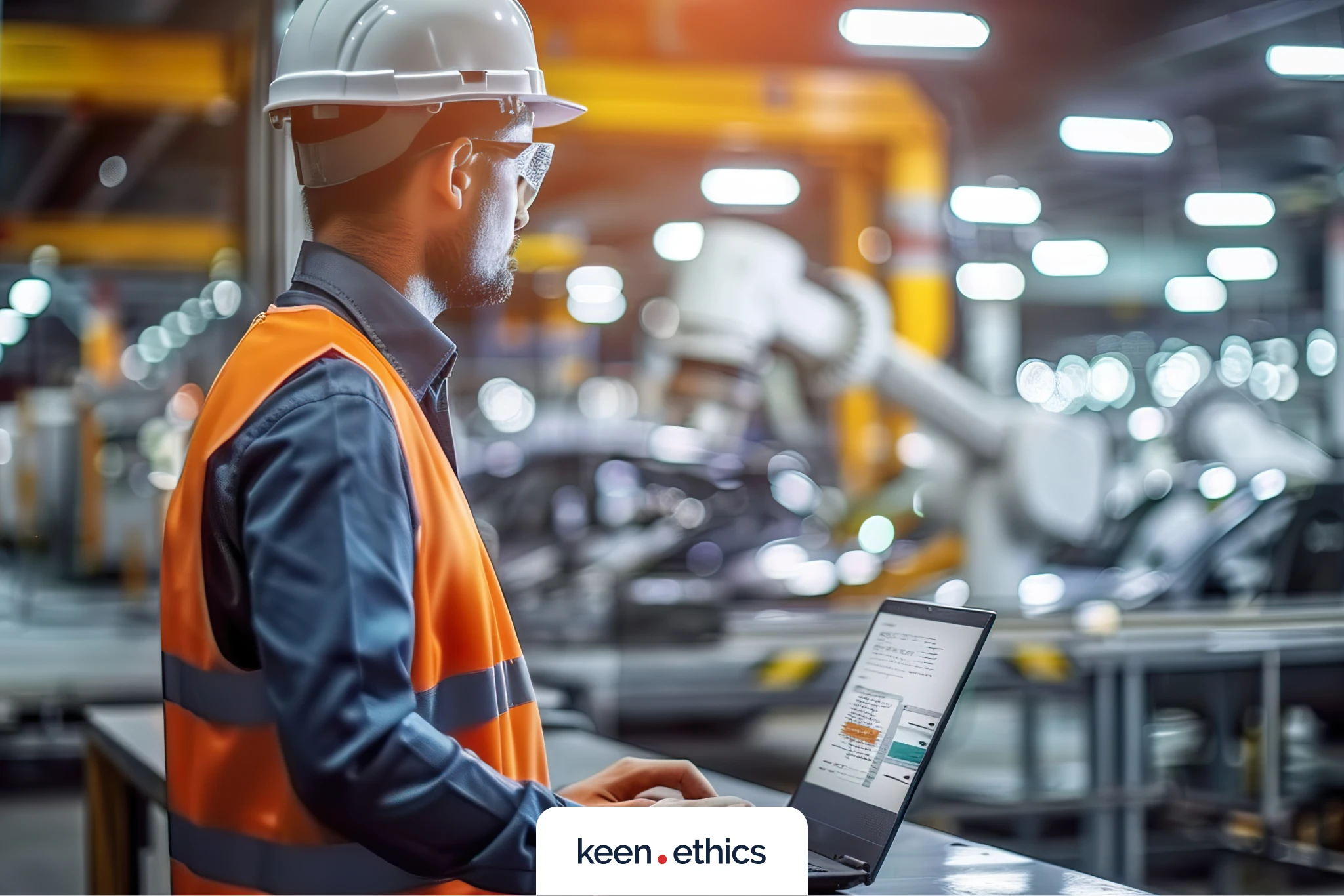
In the end, we’d also like to mention core ERP implementation challenges that arise due to the unique characteristics of manufacturing software development:
- Integrating and migrating data
- Promoting vital organizational changes
- Overcoming training and user adoption limits
- Navigating customization complexities
- Upgrading project management and governance
- Estimating the necessary time for implementation
- Performing business reengineering
- Doing testing and quality assurance
- Avoiding unrealistic expectations and scope creep
- Obtaining executive sponsorship and buy-in
We won’t dive in-depth into those details because they deserve separate articles about the unique limitations of both cloud manufacturing ERP and on-premise one. However, it’s essential to mention them since organizational aspects are the core challenge with all types of ERP software.
FAQ
What benefits can an ERP system bring in?
An ERP project can bring many major benefits. For instance, it’s capable of upgrading your ability to make predictions about certain production processes. Moreover, these systems have a strong capability to transform your general view of a company. The core goal of their implementation is to create an overarching vision of a certain business.
In what manner can an ERP system for manufacturing aid in the management of inventory?
It’s capable of collecting information on all inventory items, above all. Moreover, the systems can then trace those items across several dimensions, which include locations and even finances.
What are the impacts of ERP on production planning?
ERPs have a positive impact on production planning through features like real-time data collection and tracking. Using information collected by such systems, you can make accurate predictions about various aspects of the production process.
What’s the average implementation time for an ERP system in manufacturing?
ERP systems can take between several months and a year to implement. Everything depends on the scope of your ambitions concerning these systems and the overall size of your company.
What’s the cost of an ERP implementation?
ERP implementation costs once again depend on the scope of your firm and the complexity of the solution you want to develop. The best way to learn how much this or that system costs is to directly review your specific use case. To do this, you can address companies like ours (Keenethics), which offer full-scale business analysis to their customers.
Keenethics experts can assist!